Lean Six Sigma Belt certification
How do we akt?
As a Lean Six Sigma Master Black Belt, we can train your employees on site.
The content of the standard certification is taught using examples from the organisation and/or production on site.
The following certification is possible:
- Lean Six Sigma Yellow, Green Belt
- Lean Six Sigma Black Belt
- Lean Six Sigma Master Black Belt
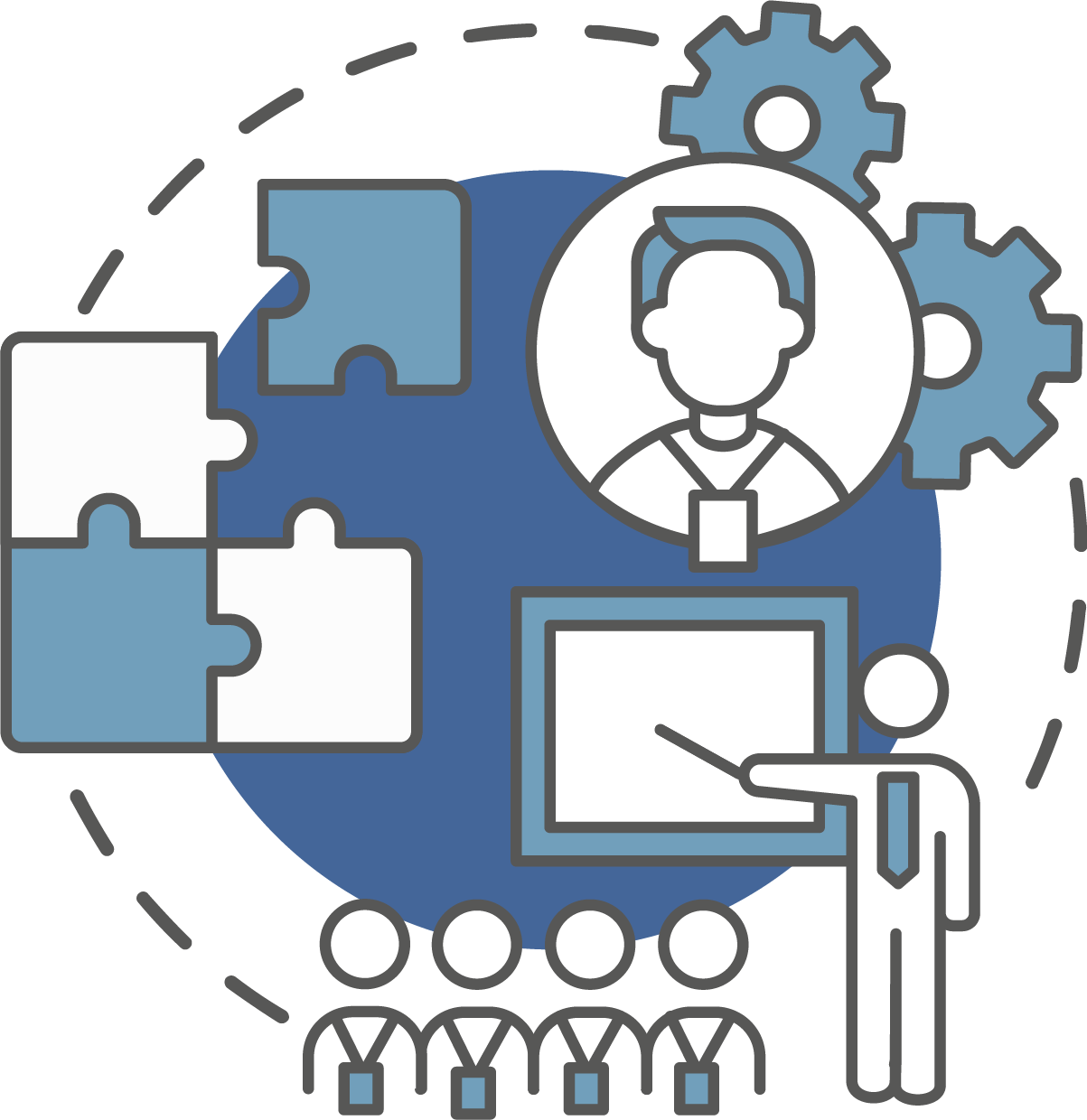
In an initial consultation, we work with you to clarify your expectations of the individual certification steps. Following the initial consultation and a visit to the organisational unit concerned, you will receive a quotation from us for your employees’ certification.
If the client’s employees do not pass the examination, the certificate cannot be issued and the examination must be repeated (maximum of 2 repetitions).
Your benefits
- If unresolved problems from your organisation and/or production are used for the practice units and may be resolved during the activity, the company benefits immediately from the certification.
- Employees have easier access to the certification content during certification.
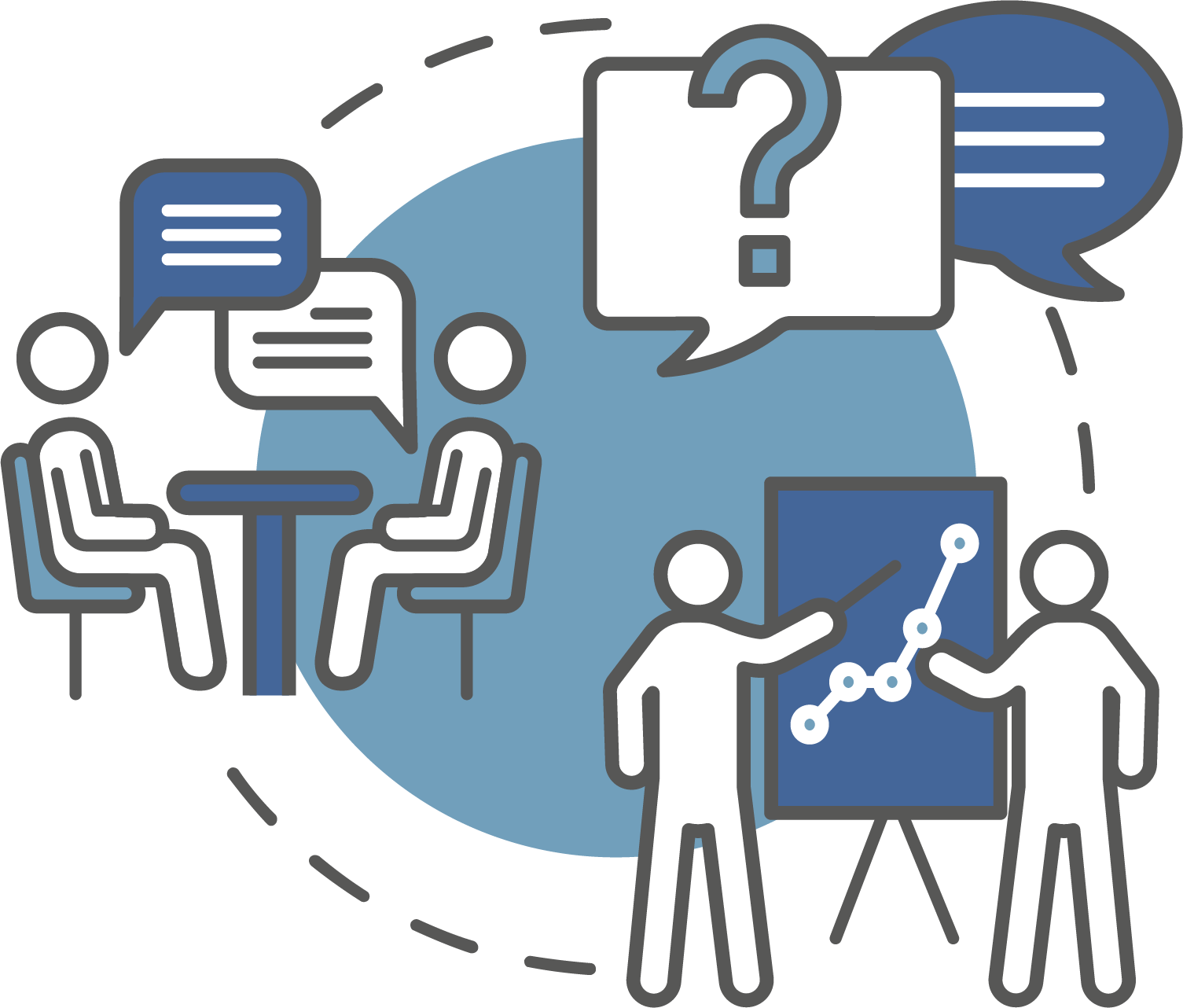